Is It Time to Replace Your Warehouse Floor? 7 Signs to Watch For
In the world of industrial operations, few things are as quietly critical as your warehouse flooring. Day in and day out, your floors endure immense abuse—from forklifts to foot traffic, chemical spills to temperature fluctuations. And in a state like Connecticut, where icy winters and humid summers stress every square inch of your facility, the need for reliable, durable flooring is non-negotiable.
Yet many warehouse owners wait too long to act, dismissing minor cracks or peeling coatings as cosmetic. The truth is, aging floors do more than look bad—they present serious safety hazards, lead to compliance issues, and chip away at your bottom line through constant repairs and lost productivity.
If you’re operating a warehouse or distribution center in Connecticut—whether in Hartford, New Haven or Fairfield County—now is the time to assess your flooring. Don’t wait until a forklift accident or OSHA citation forces your hand. Let’s uncover the top signs that it’s time for a warehouse floor replacement or epoxy floor upgrade.
Cracks, Chips, and Spalling in Warehouse Flooring
Small surface cracks may seem harmless at first. But in a high-traffic industrial setting, these are more than cosmetic blemishes. They are warning signs.
Cracks and chips often form due to repeated forklift pressure, dropped inventory, or freeze/thaw cycles that expand and contract concrete. Over time, this leads to spalling, where concrete starts flaking and breaking off in chunks.
In Connecticut’s harsh climate, the issue worsens quickly. Water seeps into cracks, freezes in winter, and expands—widening the damage. If untreated, these flaws penetrate deeper, leading to structural deterioration.
Worse still, these damaged surfaces become trip hazards and catch points for debris. Employees may slip, equipment can snag, and your facility’s efficiency takes a hit.
What starts as a hairline crack today could cost thousands in repairs tomorrow. Act early—consider an epoxy flooring upgrade to seal and reinforce your surface.
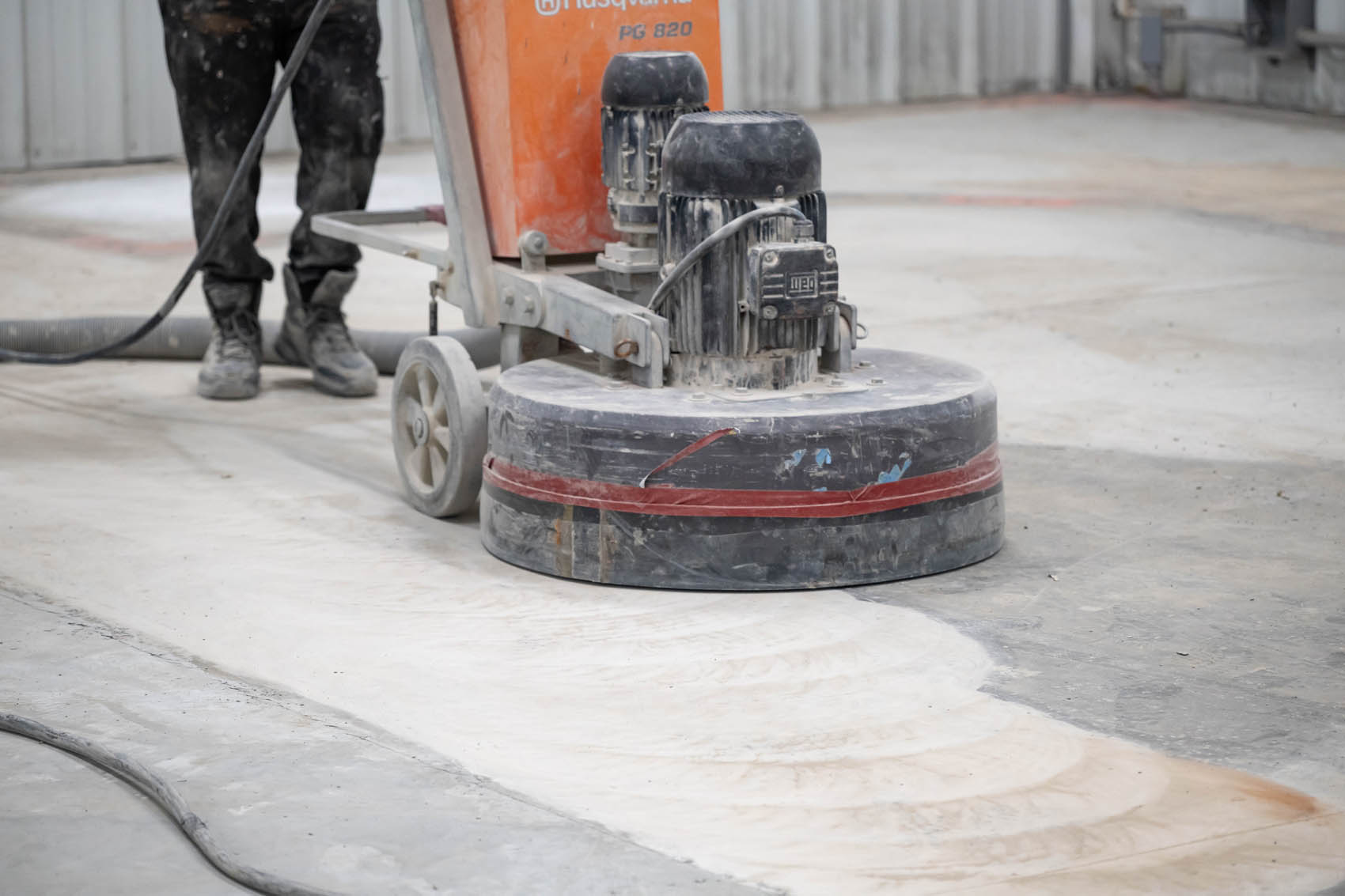
Uneven Surfaces or Settling Floors Pose Safety Risks
Have you noticed bumps, dips, or strange sloping in your warehouse floor?
Over time, concrete slabs can settle unevenly, especially in older Connecticut buildings with compromised subgrade. Moisture intrusion, poor compaction during construction, or years of vibration from machinery can cause slab movement.
This unevenness isn’t just unsightly—it’s a danger.
Forklifts can wobble or tip, pallet jacks jam, and employees are at higher risk of tripping. Not only does this create potential for injuries, but also product damage and costly operational interruptions.
Warehouse floor replacement isn’t always about aesthetics. In many cases, it’s about protecting lives, inventory, and workflows.
Have you noticed bumps, dips, or strange sloping in your warehouse floor?
Over time, concrete slabs can settle unevenly, especially in older Connecticut buildings with compromised subgrade. Moisture intrusion, poor compaction during construction, or years of vibration from machinery can cause slab movement.
This unevenness isn’t just unsightly—it’s a danger.
Forklifts can wobble or tip, pallet jacks jam, and employees are at higher risk of tripping. Not only does this create potential for injuries, but also product damage and costly operational interruptions.
Warehouse floor replacement isn’t always about aesthetics. In many cases, it’s about protecting lives, inventory, and workflows.
Peeling or Delaminated Coatings Signal Trouble
Peeling paint might be something you tolerate on your facility walls—but not on your floor.
If your epoxy or urethane coating is flaking, bubbling, or peeling, it likely signals delamination. That means the floor coating has separated from the concrete surface beneath, and your protection is gone.
Delamination is often caused by:
- Poor initial surface prep
- Moisture vapor pressure from below the slab
- Old coatings nearing the end of their lifecycle
A failing coating allows oil, chemicals, and bacteria to seep into the concrete, staining it and weakening its integrity. Plus, it’s nearly impossible to clean—posing risks for contamination and slip hazards.
Don’t wait until you’re cited in an audit. Schedule an epoxy floor upgrade and restore your floor’s durability and cleanliness.
Stains, Moisture, or Mold on Concrete Slabs
Standing water, oil stains, or mildew along your warehouse floor? These are signs your floor is absorbing and retaining contaminants—never a good thing.
Moisture and porosity issues are common in Connecticut due to the high water table and humid summers. Without a non-porous epoxy floor, your slab becomes a sponge. Over time, this can lead to:
- Bacteria or mold growth
- OSHA or USDA violations
- Structural weakening from internal moisture
Facilities storing food, pharmaceuticals, or chemicals are especially at risk. A moisture-resistant epoxy floor upgrade helps prevent these costly problems and supports USDA compliance.
Difficult to Clean or Maintain Floors Waste Time
Older concrete floors, particularly those worn or unsealed, are magnets for dust, grime, and spills. The longer they’ve been in use, the harder they are to keep clean.
And with Connecticut’s seasonal sludge, salt, and moisture, cleaning inefficiencies only grow.
Modern flooring solutions—like polished concrete or easy-to-clean epoxy floors—offer non-porous, smooth surfaces that require minimal labor. No more pressure washing, scrubbing oil spots, or chasing dust.
Everlast Industrial Flooring specializes in Connecticut epoxy contractors who install low-maintenance flooring systems that save you time and labor every day.
Frequent Downtime for Repairs Impacts Business
Are you patching your floors every few months? Each maintenance window means downtime, re-routing inventory, and lost productivity.
Eventually, these small fixes snowball into major inefficiencies.
Rather than investing in recurring patchwork, consider a full warehouse floor replacement with modern, fast-curing epoxy systems. These allow installation with minimal disruption and long-lasting durability.
Everlast’s rapid-install technologies mean your operations can resume faster—without cutting corners.
OSHA or Compliance Issues from Old Flooring
Your floor could be the reason you fail your next OSHA or USDA audit.
Old or degraded flooring often lacks:
- Proper anti-slip ratings
- Clearly marked safety zones
- Appropriate drainage
- Chemical resistance
For example, facilities that handle hazardous materials must meet specific flooring standards for containment. Likewise, warehouses with foot traffic need traction-certified surfaces.
A compliant safety epoxy floor can include everything from slip-resistant textures to color-coded zones for forklift lanes and pedestrian paths.
Don’t Let a Failing Floor Cost You More
Your floor is the foundation—literally—of your warehouse operations. Ignoring its decline isn’t just a cosmetic issue. It’s a risk to your business, your employees, and your customers.
Whether you’re dealing with cracks, constant repairs, or compliance issues, it’s time to stop patching and start planning.
Serving Hartford County, New Haven County, Fairfield County, Windam County, Tolland County, New London County, Middlesex County, Litchfield County, Everlast Industrial Flooring offers expert assessments and epoxy floor upgrades tailored for Connecticut’s demanding industrial needs.
Book your free warehouse flooring inspection today.
Frequently Asked Questions
Can epoxy floors handle heavy forklift traffic?
Absolutely. Industrial-grade epoxy floors are engineered to withstand constant pressure, abrasion, and impact from forklifts and other machinery.
What are the benefits of epoxy over regular concrete?
Epoxy is non-porous, slip-resistant, easy to clean, and highly durable—making it ideal for industrial environments.
Is epoxy flooring safe for food storage warehouses?
Yes. USDA-compliant epoxy systems are available and ideal for food and beverage storage facilities.
How much does warehouse floor replacement cost?
Costs vary based on square footage and condition, but epoxy solutions are a cost-effective investment compared to recurring repairs.
Can you apply epoxy over old concrete?
Yes, but the existing surface must be properly prepared. This will involve cleaning, grinding the substrate by method of diamond grinding and or shotblasting and proper moisture testing.